Click Selections Below
to View
Our New Jewelry Line
|
|
|
|
|
|
|
All of the items in Skystone Designs section are done by a casting method, opposed to handmade, that is done in our Navajo Section.
The important part of this section is, that we are presenting and selling, like in our Navajo Section, our own
product. Each item from the beginning to the end, is made in our shop, and all is designed by Skystone Creations.
The end finish of each piece is done by our Navajo Silversmiths. All items like: Pins, Pendants, Rings, Bracelets,
Earrings, Bolas and Buckles, and Crosses are made out of Sterling Silver.
What do we need to know about Casting and Metals?
For most people, the pleasure of making jewelry comes from time spent at a workbench, actively driving tools to
cut, bend and assemble a piece. Metals are made of crystals that arrange themselves in a regular pattern called
a lattice. This has a lot to do with the physical properties of a metal. Metals with the same crystal lattice will
probably have similar density, malleability, conductivity, and so on. Crystals, also called grains, are clusters
of molecules gathered into units whose structure determines the ability of metal to bend, conduct heat and reflect
light. All of these attributes are important to jewelers.
When grains are small, a sample will be harder to bend, more likely to break, tougher, and a better conductor of
electricity. Large crystals make a metal more responsive to patinas and more malleable, except when the grains
are very large, which causes the metal to become tough again. The usual way grains become small is through hammering
or rolling. Do this enough and a sample of metal will eventually break, as the grain boundaries become too small
to hold the piece intact. This process is called work hardening. Its opposite, annealing, uses heat to recrystallize
the internal structure, building large grains from small ones. All of this goes on at a microscopic level.
Annealing temperatures vary with each metal and alloy, but as a rule of thumb they are about two-thirds the melting
temperature of a pure metal. Annealing can be done as often as necessary.
The CASTING
By far the most common form of casting in contemporary jewelry making is lost wax waste mold centrifugal casting.
It's a long name, but worth understanding because it tells us a lot about the process. The word wax tells us the
model, or replica, is made of wax, while lost refers to the fact that the model will disappear somewhere along
the way. Each model can be used just once. The waste mold part of the name tells us this is true of the mold as
well - it too must be destroyed (or "wasted") to retrieve the casting.
Like the model, this mold can be used only once. We know that some metals, including silver and gold, will draw
up into a sphere when heated. This explains why gravity alone is not sufficient to fill a large, detailed mold.
And here the word centrifugal tells us what kind of force is used to push the molten metal into the cavity. Lost
wax. Waste mold. Centrifugal casting.
LOST WAX CASTING
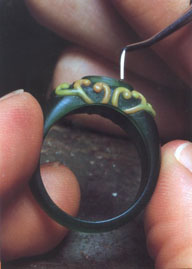 |
Making a master model look exactly like the intended design is one of the most difficult
challenges faced by the model maker. For one thing, the master has to be made larger than the intended finished
piece to accommodate shrinkage. In addition, things look quite a bit different on paper than they do in metal.
Model making can be viewed as an exercise in intelligent compromise. The model maker must find an acceptable middle
ground between what the designer wants and what can be done within the limits of casting. The best results can
be achieved when all parties involved understand those limitations. |
FITTING THE MOLD
Natural rubber or silicone rubber? In the world of lost-wax casting, this question is hardly
an academic one. The mold material chosen must be up to the task of turning a single original model into hundreds
or even thousands of wax models for casting, and choosing the wrong material can lead to some serious hair - pulling
in the casting department.
There are actually three primary categories of rubber mold making materials: natural rubber, vulcanizing silicone
rubbers, and room temperature vulcanizing (RTV) rubbers, a non - shrinking, no - heat option. Each has its advantages
and disadvantages, and as a result, each may be the best choice in certain situations. The key to choosing between
them is to understand the properties of all three, and then decide which to use based on what qualities are most
important for a given situation.
Whatever your choice for mold making, you'll need to use the right tools and techniques to get the best possible
results. When cutting molds, be sure to use a sharp blade, and replace it immediately if it gets nicked or dull.
Make sure your hands are clean and that the model has no visible defects. |
|
BUILDING THE BETTER TREE
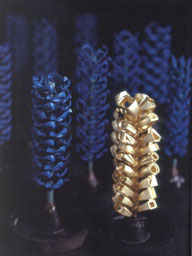 |
Pattern alignment is often a matter of choice. Some casters prefer to stagger the rows so
they can pack the pieces more tightly. Others prefer a straight alignment, which causes less turbulence in the
main sprue. Product design will often dictate which alignment style is most suitable. People clipping the patterns
from the tree will also have opinions regarding which alignment is best, at least from their standpoint, but keep
in mind that casting successfully is the primary concern. |
INVESTMENT
More than 70 million pounds of investment powder is used worldwide each year by lost - wax
casters in the jewelry
industry. Yet all powders are not created equal. While the major investment manufacturers in North America, Europe,
and
and Asia all aim for high quality, casters should understand that some powders are truly premium, while others
are
tailored for casting base metals. Ultimately, the investment's performance depends on the particular composition
of ingredients, and on how well casters use - or, more important, misuse - their powder.
Casting manufacturers should have in place an adequate ventilation/exhaust system that eliminates powder inhalation
by workers. The microscopic particles cannot be seen by the human eye, but they are present. Workers can also protect
themselves by wearing respirators while working around the powder. |
THE BURNOUT OF WAX
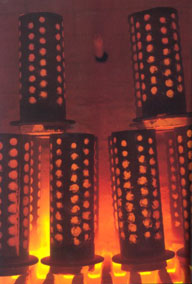 |
The burnout of wax happens in hidden cavities of the set investment; if problems occur during
this phase, they will become apparent only after the tree has been broken out. |
CASTING
After burnout, you're ready to cast. Gold, Sterling and other metals used for models and
samples ( in fact, all metals other than platinum) enjoy the ability to be cast in the same equipment, since the
maximum melting temperature will be 2,100 F. However, if you casting platinum - for which the melting temperatures
can reach 3,200F - you will need special high - temperature equipment. Vacuum casting has become very common these
days - even very small shops often go with it. Vacuum is a method through which ordinary gravity is used to vacuum
out air from under the perforated flask and to help move the air and gases from under the incoming casting alloy. |
|
METALS and ALLOYS
This is a huge topic, even taken quickly, so we'll confine ourselves to metals used by beginning jewelry makers:
copper, brass, silver and gold. Three of these are pure metals, while one, brass, is a mixture, or alloy, of two
metals. Pure metals, also called fine, are often too soft for wearable jewelry, so they are alloyed as well.
PRECIOUS METALS
Fine gold is given the arbitrary designation "24," so we can say that of 24 parts, all 24 are gold. In
the case of 18-karat gold, 18 of the 24 parts are gold, with the balancebeing something of lesser value. If you
write this as a fraction, 18/24, and reduce it, you'll see that 18-karat gold is three-fourths gold andone fourth
something else. Generally speaking, alloys of 18K and purer are called high-karat golds.
The additive ingredients in alloys are used to affect the color, strength, ductility and value of the resulting
alloy. In the case of yellow gold, equal parts of silver and copper are added. Rose gold ( also called pink gold
) is made by increasing the proportion of copper, and green gold is made by increasing the percentage of silver.
Note that in all colors the proportion of gold remains the same. The most popular gold alloy for jewelry in the
United States is 14 karat, which is also written as .585, or 58.5 percent gold. The balance can be anything, but
it is usually some combination of silver and copper, except in the case of white gold, where platinum, palladium
and nickel are used to change the color.
Pure silver is occasionally used in jewelry components, particularly when malleability is an asset. This us the
case with bezels, which need to be safely pressed down againstgem. For most applications, however, fine silver
is too soft, so a small amount of copper is added for strength. Hundreds of years ago, it was determined that the
addition of 7 1/2 percent copper created a metal strong enough to stand up to use while retaining the warm shine
of silver. This alloy came to be called sterling, and it is far and away the most commonly used silver alloy for
jewelry.
A slightly baser alloy that contains 10 percent copper was used for hundreds of years in coins, and is therefore
called coin silver. It is rarely seen today,, except in older pieces. Coins minted in the United States have not
contained silver since 1966.
BASE METALS
Copper is used in jewelry for its color, which is orange when polished, brown with normal wear, and green or blue
after exposure to certain atmospheres. It is inexpensive, malleable, resilient and attractive, but its one shortcoming
is the fact that copper not only discolors when worn, but discolors the wearer as well - typically by turning skin
green. This is because of copper's eagerness to combine with almost any element that passes by, from oxygen to
ammonia. Despite these shortcomings, jewelers value copper for its colors; it is usually patinated and sealed to
protect the metal from further corrosion. Because its melleability is similar to sterling, it also makes an excellent
practice material. It is slightly more difficult to solder because of its tendency to oxidize, but this means that
a person who has mastered soldering by experimenting with copper will find the transition to sterling especially
easy.
Another of copper's virtues is its affinity with other metals. As described above, copper is used to strengthen
gold and silver. When alloyed with the low-melting gray metal called zinc, copper pulls a magician's trick to yeld
a metal - brass - that is yellow and has a higher melting point than either of it constituents. By definition,
brass is a mixture of copper and zinc, but the proportions can vary and will yield a wide range of results. The
most common mix, called yellow brass, or CDA 260, is 30 percent zinc and 70 percent copper. As the proportion of
copper increases, the color becomes more golden and the metal more malleable. An alloy of about 88 percent copper
called NuGold is widely used in jewelry making, as are other low-zinc brasses.
Nickel silver, also called German silver, deserves mention not only because it is useful in jewelry, but because
its name is so misleading. It contains no silver, and does not come from Germany. It is an alloy of copper, zinc
and the element nickel. To see what it looks like, search your pocket change for a 5 cent piece. We should call
this alloy " white brass " because it is so similar to yellow brass in cost, malleability, and the way
it solders. |